Tuesday 4 November 2025 | 14:00 - 17:00 CET | Barcelona, Spain
Workshop Agenda
13:30 - Workshop registration / refreshments
14:00 - Workshop Introduction
14:15 - Introduction to rCB
- This session will explain rCB in easy terms also to non-technical colleagues, investors and everyone attending Recovered Carbon Black Europe for the first time.
- Why does rCB unlock business viability of tyre pyrolysis technology?
- How does curating ELT feedstocks help rCB production?
- Is rCB a commodity yet?
- Can it be sold?
- What is the supply & demand and who are the customers?
- We will cover all of these questions and of course any other questions you might have.
15:00 - Current state of rCB
- This session will analyse the current state, show mega-trends in the industry and give company success stories and application examples.
- rCB terminology, standards and specifications, which are currently under review in the June ASTM meetings, will be important topics.
- We will also invite rCB companies in the audience to briefly introduce themselves to the workshop community.
15:45 - Refreshment Break
16:00 - Future of rCB
- Here we will discuss new technologies, new concepts, new applications and new ideas, such as ELT feedstock sorting, ash leaching, activation and new process technologies.
- It will again be possible to contribute your innovation and to introduce your company on the day.
16:45 - Q&A
17:00 - End of Workshop
More presenters will be announced soon, if you have some words to say or want to introduce yourself in the workshop as an attendee, we will have microphones for that!
Tickets are €449 in-conjunction with your conference ticket!
Speakers
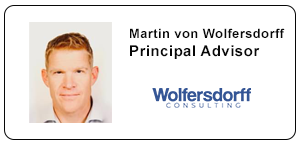